Weighing the Risks of Regulatory Non-Compliance
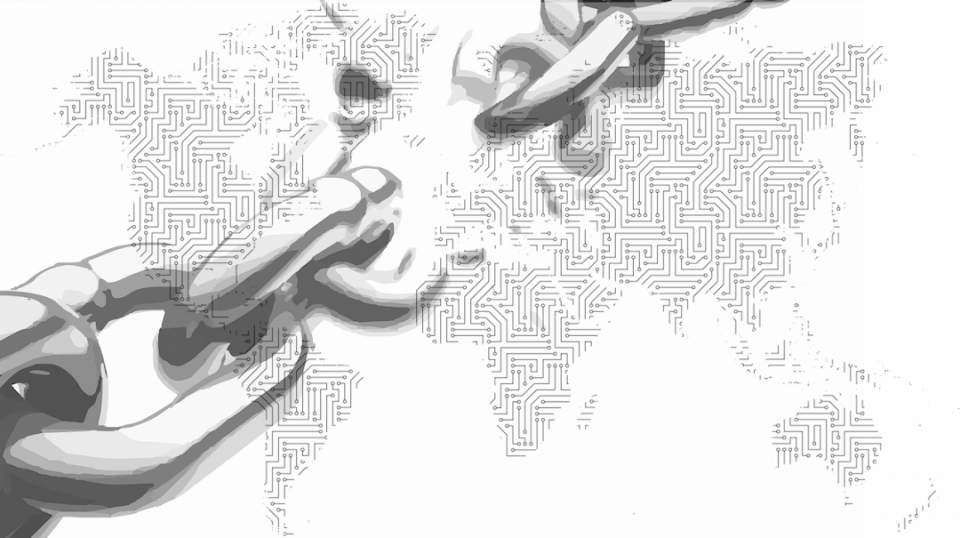
By Liz Parent, Director Sales & Marketing, Testing Partners
For various reasons, manufacturers often choose not to obtain required wireless, safety and environmental compliance certifications for their devices going into global markets. Maybe testing and certification are too costly, and they already have orders to ship; they’re only shipping a few devices here and there and it’s not “worth it” to deal with the challenges of regulatory compliance; they didn’t know regulatory compliance even existed; or they think their product is safe, but without evidence, this could be futile.
While all these reasons might seem valid, the risks of non-compliance can far outweigh the certification costs for global markets. We all agree that sales revenue is top priority in manufacturing processes (or what’s the point, right?), however, thinking long-term plays a huge role in a company’s overall success and teaches the entire team—from marketing to sales to engineering—the benefits of being proactive instead of reactive.
What are the risks? When a product hasn’t been properly tested by an accredited lab, the safety risks to the consumer increase. This could result in product recalls, costing the manufacturer tens of thousands of dollars from product being removed from shelves, losing consumer confidence and even causing harm to the consumer.
The United States Consumer Product Safety Commission (CPSC) is a governmental agency that regularly posts product recalls on their website. These recalls are not limited to small companies—they include multinational corporations who produce tens of thousands of units per year and end up having to recall those units if their product is reported unsafe. This results in the issuance of full refunds to consumers, loss of profit and credibility from retailers and distributors, loss of consumer confidence in the product and consumer safety hazards that could result in fire hazard, strangulation, burns and other risks, including death. Many companies never bounce back from the damage done to branded products and end up going bankrupt or out of business. Proper safety testing (and quality assurance measures) can drastically minimize these risks.
Another thing to consider is that Customs can charge fees to hold product that doesn’t have proper certification documents when entering the country, or product could be returned or destroyed at the manufacturer’s cost. Adding to the challenge, many countries are currently cracking down in this area. International regulations for type approval and safety certifications were put into place for each country with varying language. The purpose of a regulation in one country might be to dictate radiofrequency band usage or electrical limits, for example. A manufacturer can go a lifetime without violating a regulation like this, and technically, be compliant with the law.
However, the fact that a country has a regulation isn’t the end of the regulation. It’s actually stating that certification must be obtained proving the manufacturer is not violating specific terms of the regulation. If certification is not obtained, and the manufacturer has product that falls within the scope of the regulation and the authority checks for certification, the manufacturer will be held accountable for violation, often resulting in large fines.
Some countries check documentation at Customs, and their regulations are written in a way that dictates this. Meanwhile, other countries don’t detail enforcement in writing, and manufacturers often use this as an opportunity to ship without product certification.
It’s always best for manufacturers to assume that because regulations for certification exist, there are risks involved if certification is not obtained, and it’s a gamble they must decide if they are willing to take. Spending money on testing and certification will bring peace of mind, consumer safety and confidence in knowing you are compliant with certification regulations.
If not knowing each country’s regulations keeps you from obtaining the necessary certifications, or you don’t know how to design/build a product that will be compliant with global regulations, that’s the time to pick up the phone and call your World Trade Center NorCal rep and get the conversation going.
About Testing Partners
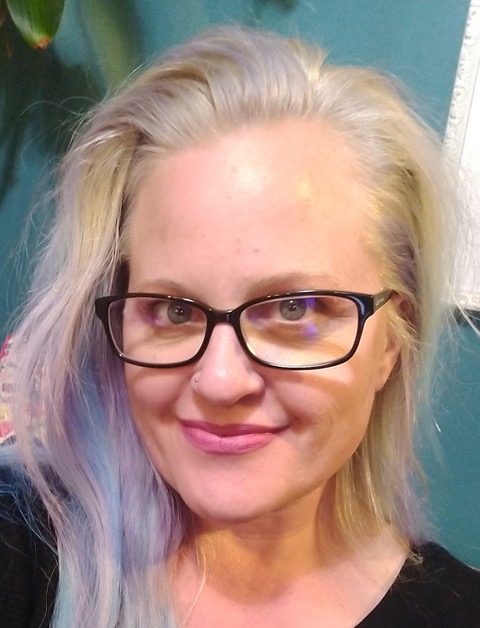
Testing Partners was founded as a result of Managing Director Jeff Baum working in compliance certification for over 25 years for major labs. He noticed there was a gap in the industry, in which over 90% of the products sent to the labs for testing were failing their initial tests because the products weren’t properly prepared for meeting regulatory standards, costing clients extended time in the labs and thousands of dollars in extra testing costs. He found that by offering pre-compliance and product construction reviews, fewer products were failing testing, saving 2-3 months in lab time and thousands of dollars in repeat testing costs, and keeping market launches on schedule. Testing Partners offers subject matter expertise in all fields that require regulatory compliance: medical, automotive, aviation, industrial, cellular, electric, wireless, IoT, ATEX, hazardous locations, children’s toys, textiles, PPE and more, from startups to multinational corporations.